Dry sump so needs a tank FFS, not even thought about this, ordered an original from eBay to get me out of the doo-doo and it’s an ugly beast to say the least…, for some reason it does’nt fit perfectly with how I have changed the layout of the frame, back to the drawing board for me.
So, my thought are now I can make something that does not look so out of place, tucked up under the seat as best we can, space to mount the cdi on top and far enough away from the carbs not to get in the way when we build filters.
Time for some choppy choppy with cardboard and sticky tape, try to get a rough idea of how it might fit and try to get a similar volume or even a bit larger.
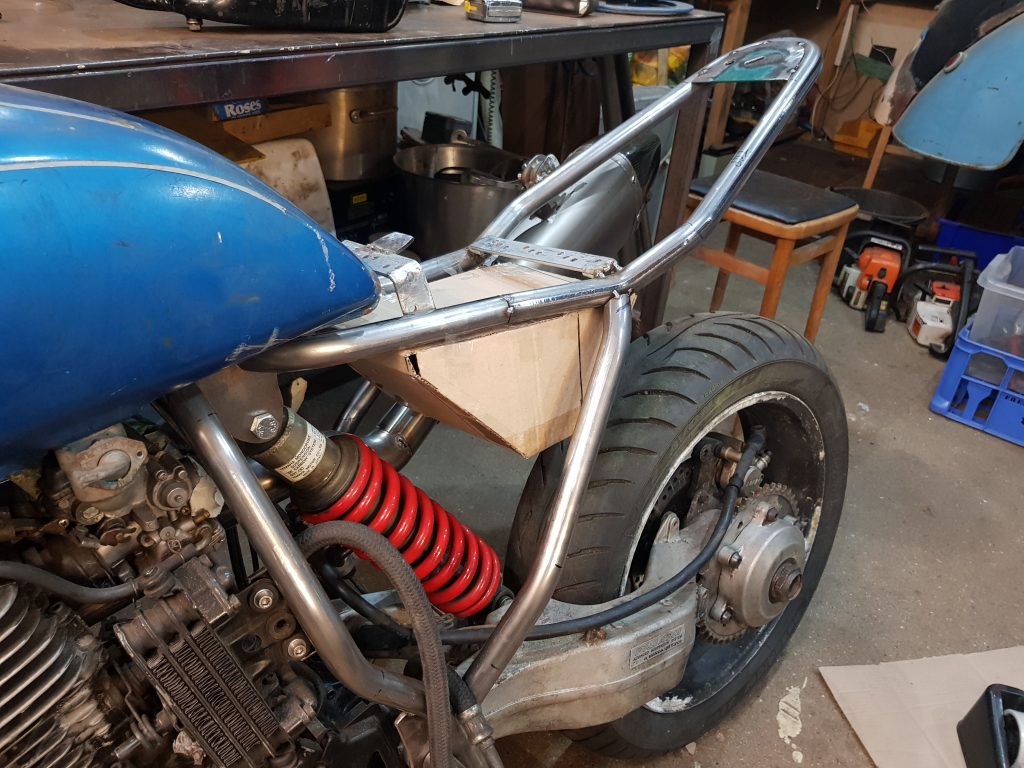
I’ve tried to work out volume and think this cardboard mock up is much bigger than it needs to be so I’ll chop it down a bit then make a metal version.
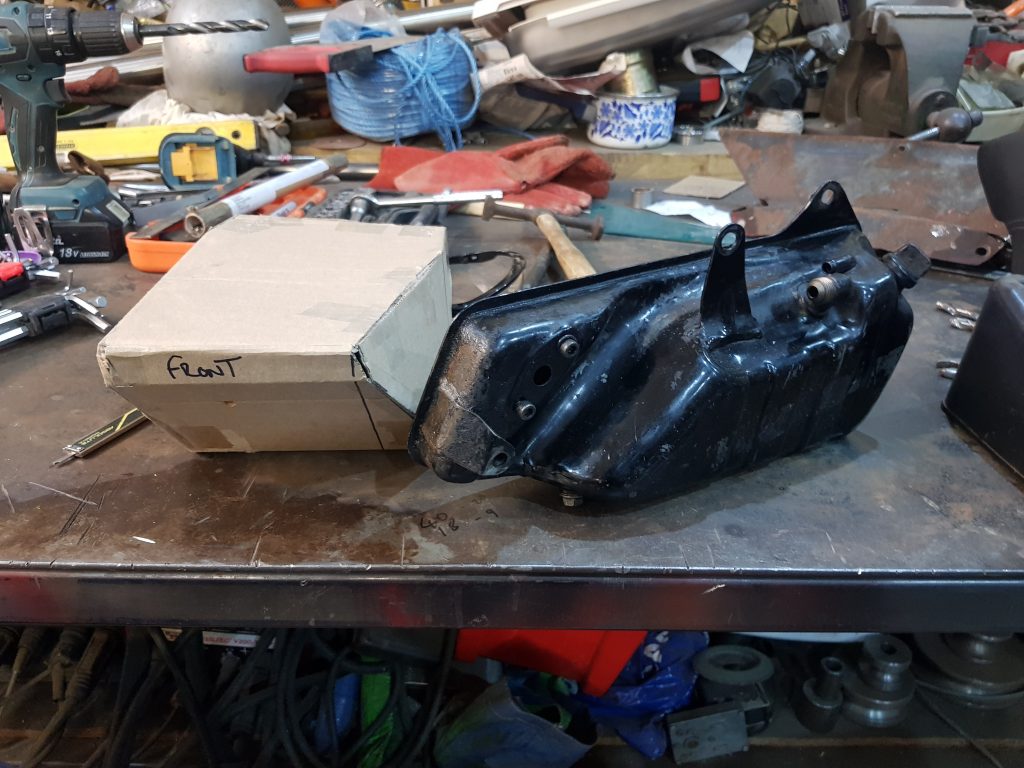
Looks a fair bit different to the original..
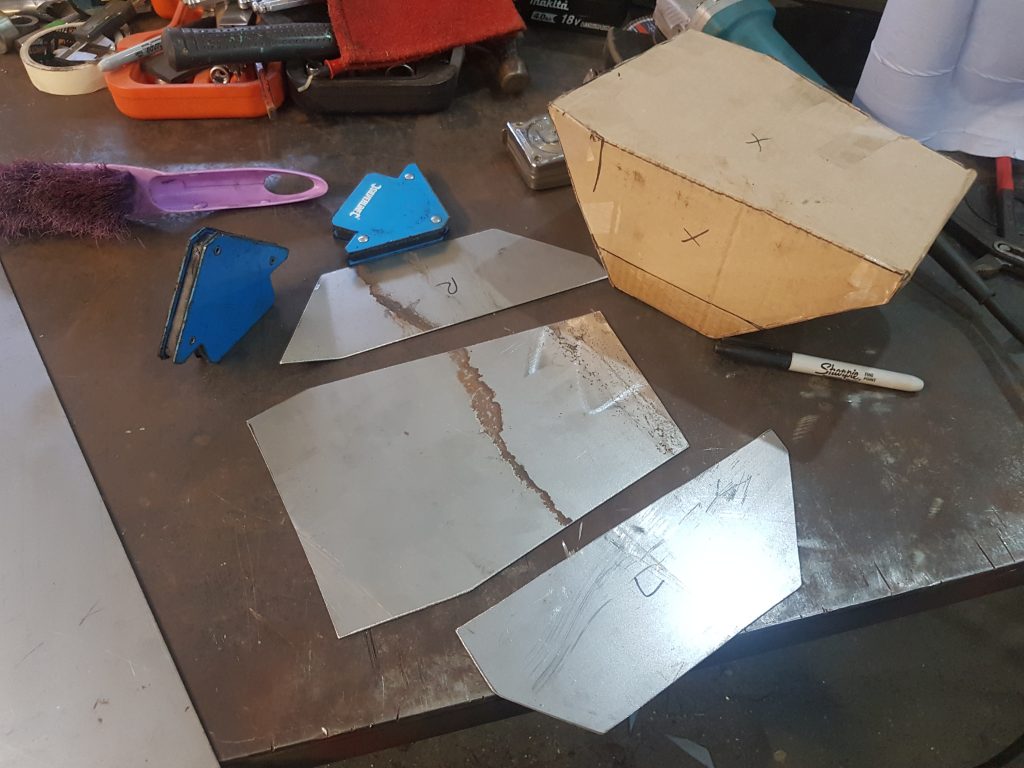
Draw around the box and transfer it to steel plate, I’m using 1.6mm as I have some in stock. I have reduced the size as per the line on the card box. Next we need to bend the plates prior to welding, we use a ‘state of the art’ bending machine to get exact bends.
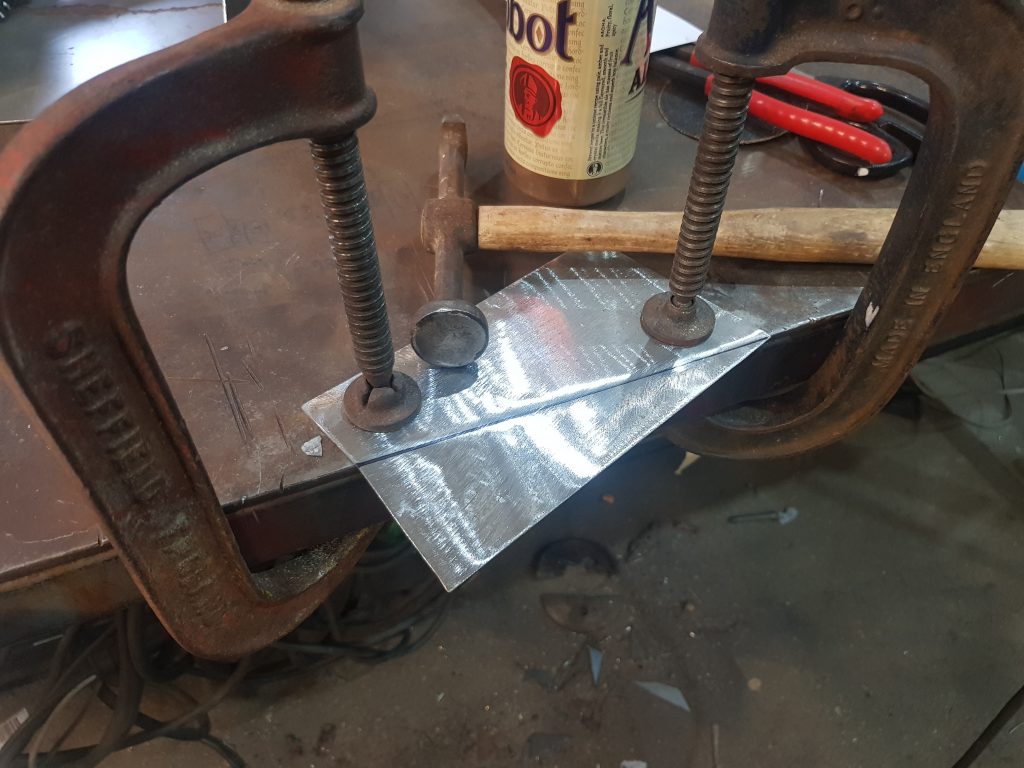
Ok, so the Scavengers have yet to get a bending machine so we just G-clamp stuff to the bench and whack it with a big hammer, similar results. Next we need to tack the parts together.
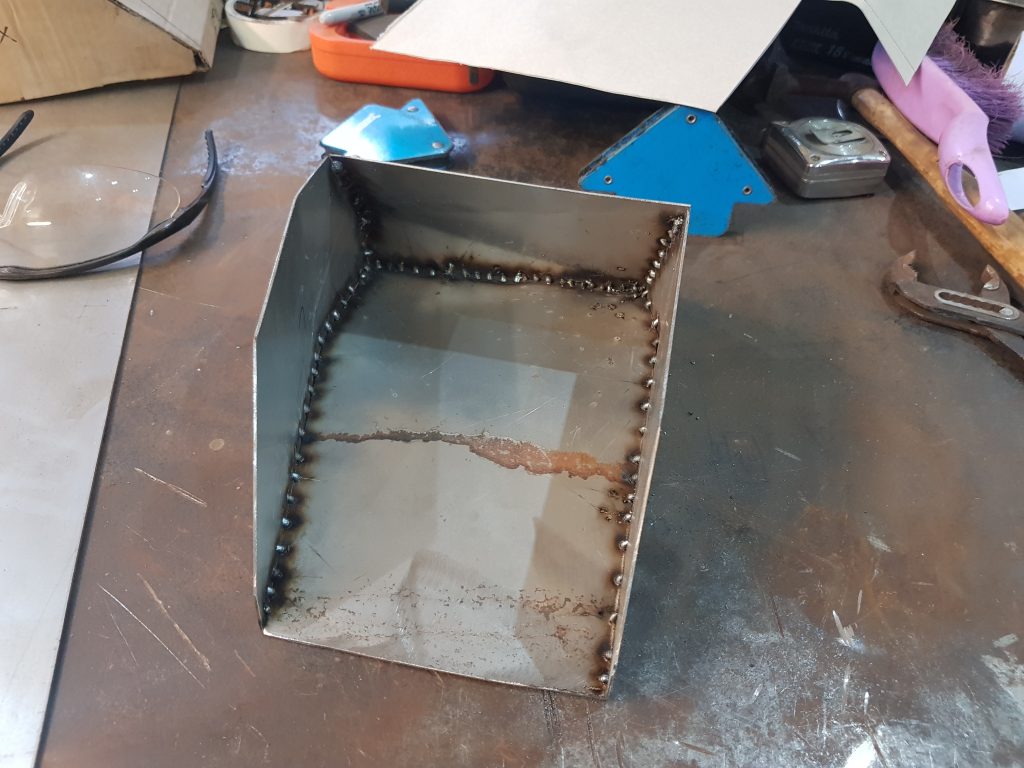
The plan is to tack on the inside with the mig welder as it’s quick and easy and when finished seam weld the outside with the tig welder to get an oil tight seal, failing that just get a really thick powder coat….JOKING
Finished up for the night and for some reason I shone my torch back in the workshop…WOW….I have been breathing this in all night, no wonder I get shed bogies.
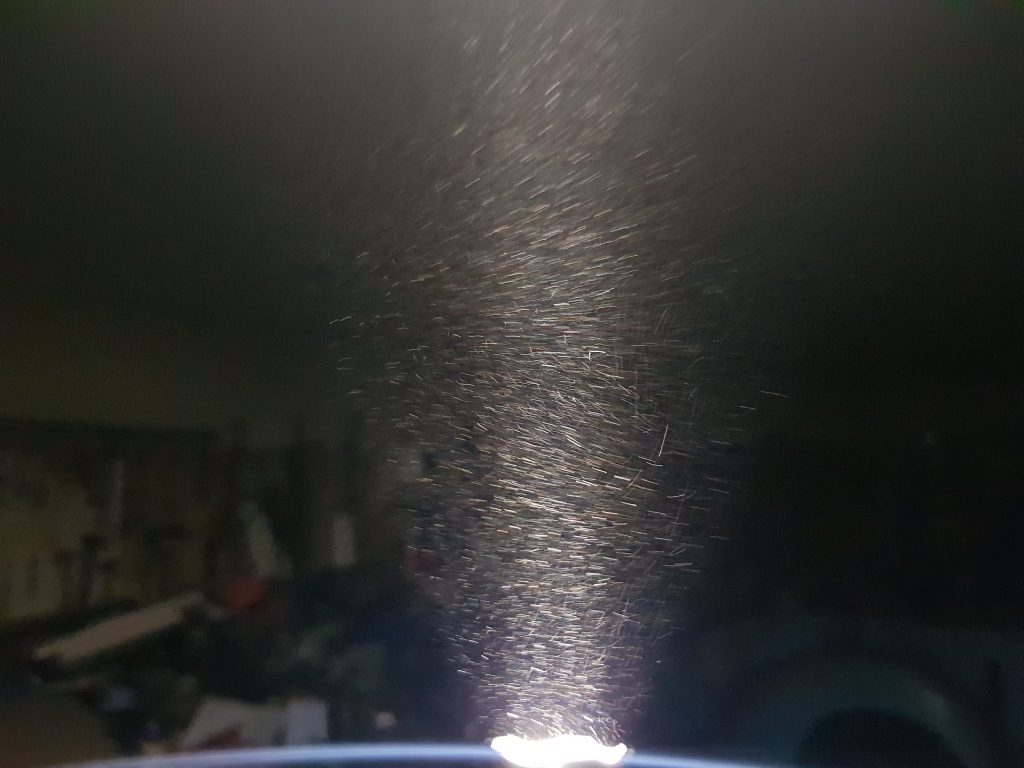
Next job is to procure an oil feed fitting, the threaded elbow you can see, I am lucky enough to live near some racing companies that stock this sort of thing so this should be easy! OK, not so easy as it turns out, it’s not a standard pipe thread, it’s metric…grrr
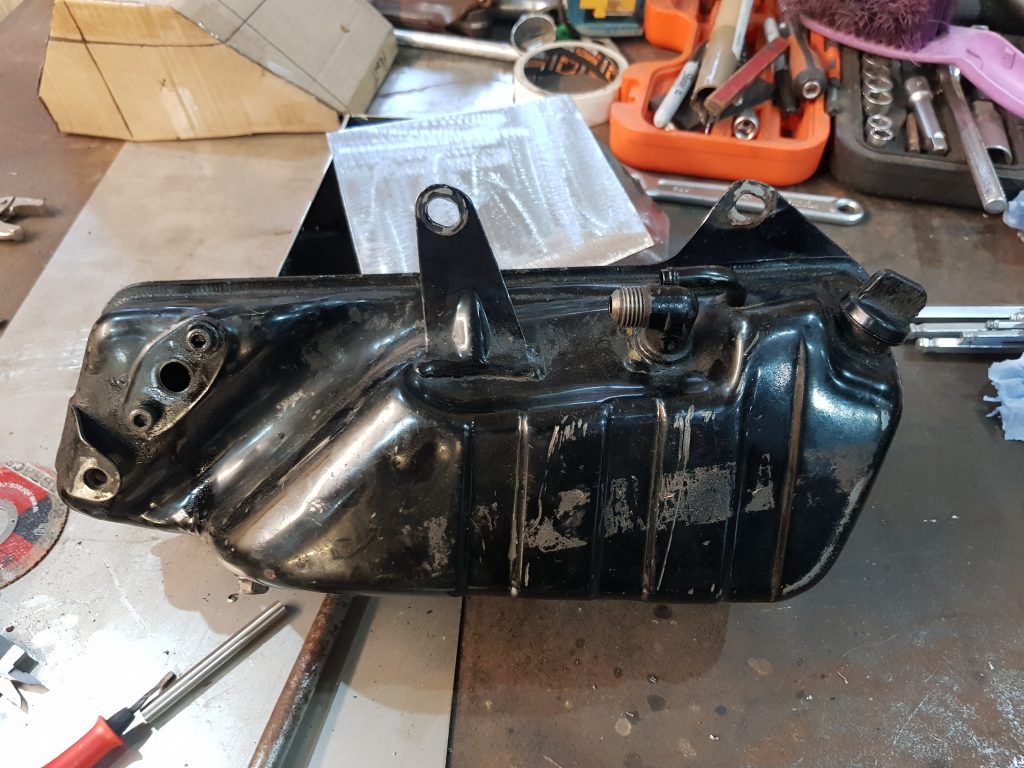
I’m loathed to cut up this tank just to get a fitting out and I’m struggling to buy one but… I have just found an M16x1.5 die in my drawer that I bought for some use on the XS project so I can now make one!!
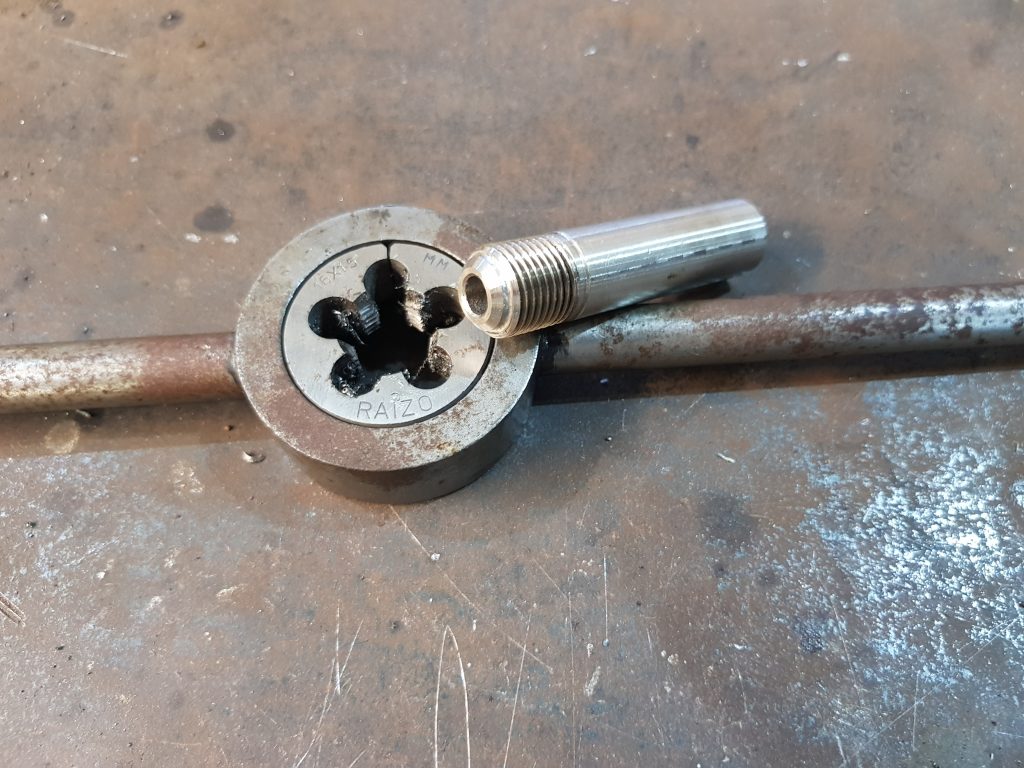
I have bored a 6mm hole all the way through and added the thread just need to make the 45 degree angle.
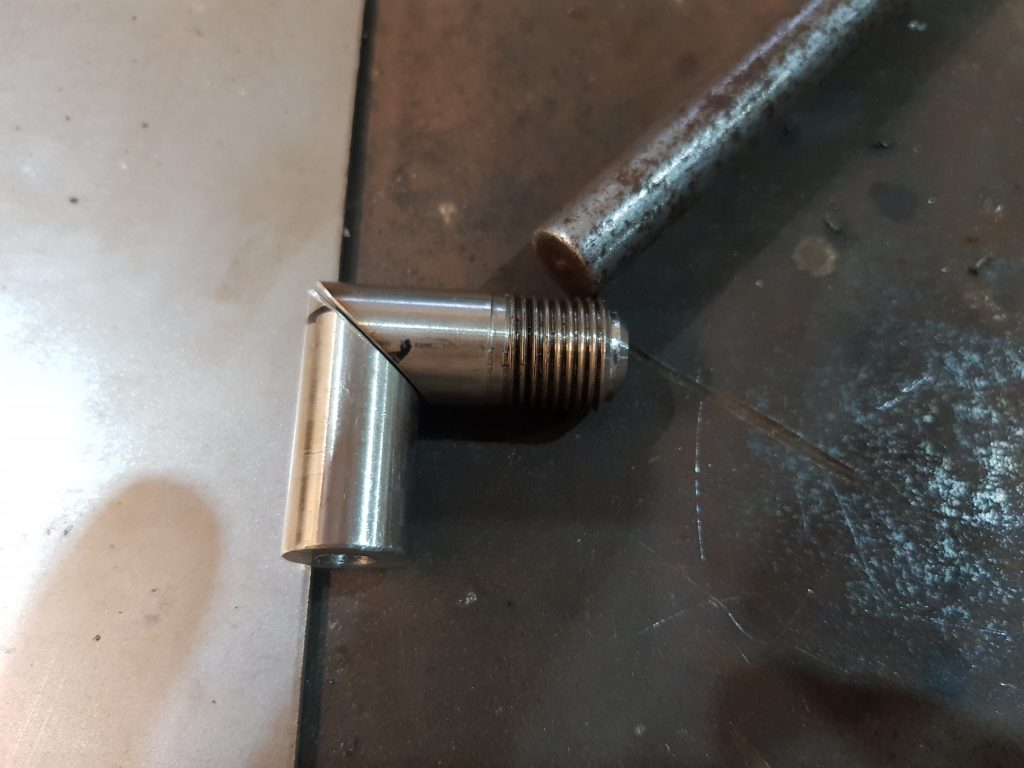
To make the cut I used the scavengers water jet cutting machine, the burn marks you see on the cut are from water and not where it was G-clamped to the bench and attacked with a grinder by eye in the hope the cut would be somewhere near where we needed it. Yee-Haw..
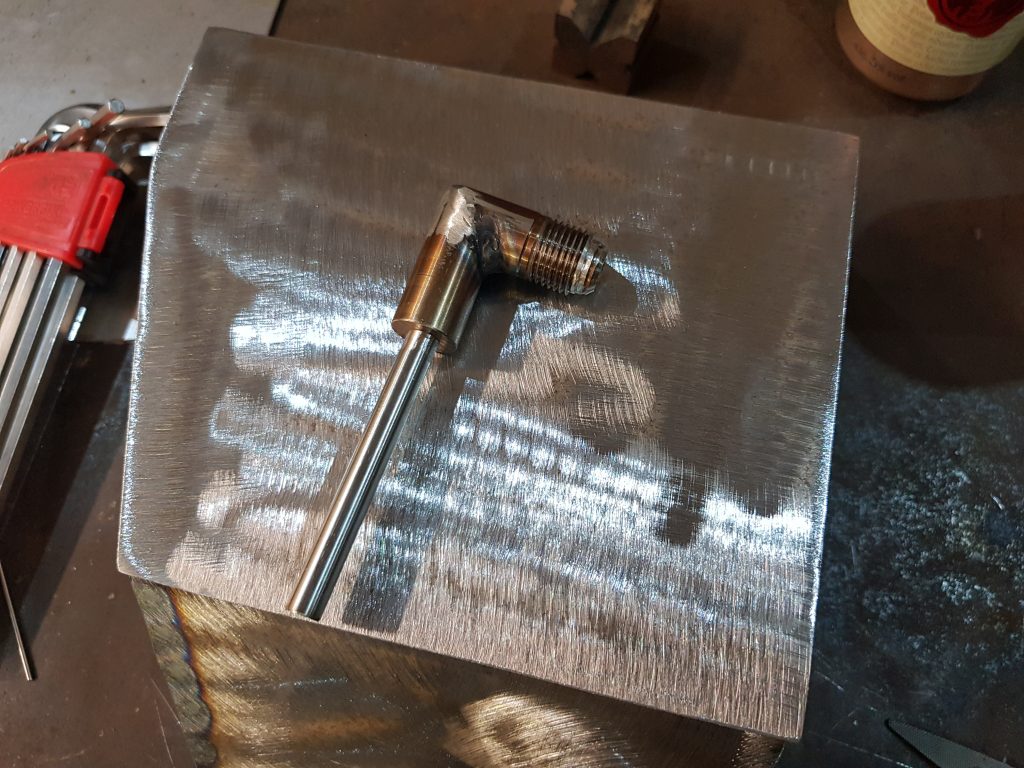
Once seam welded with the tig and ground off the excess bits it looks alright, need to weld this in place but I’m going to hang fire here a bit as there is some slack in the connecting pipe so I don’t need to commit just yet, I’ll wait untill the cdi is mounted and see how it looks.
Update….so I, for some drunken unknown reason decided to go ahead and weld the elbow in place exactly where it looked like it should go from the bench rather than on the bike….
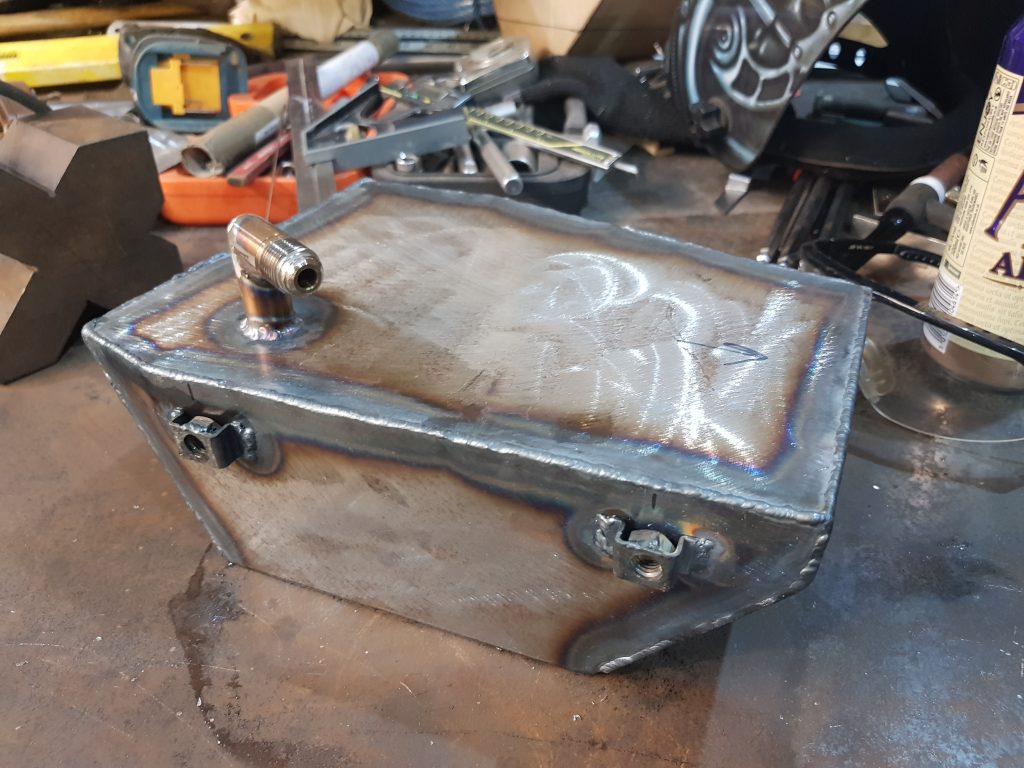
Looks alright, you can see the long weld closest to camera, this runs in line with the frame so even a stoned monkey could figure out when I add a fitting to the elbow it’s going to hit the bloody frame, one of those moments, all adds to experience though.
Interesting story/fact, when I went to night skool to learn about engineering one of the things that has stuck in my head over the years is something told to me by the tutor (Jack), ‘It’s not a problem making a mistake, it’s how you get out of it that counts.’ wise words from a very clever man.
There is not a lot of room but as it turns out a new 1mm slitting disc in the grinder can just about reach so I started to trim away the welds, went as deep as I dared and then used a large wrench to rotate the elbow to get it free.
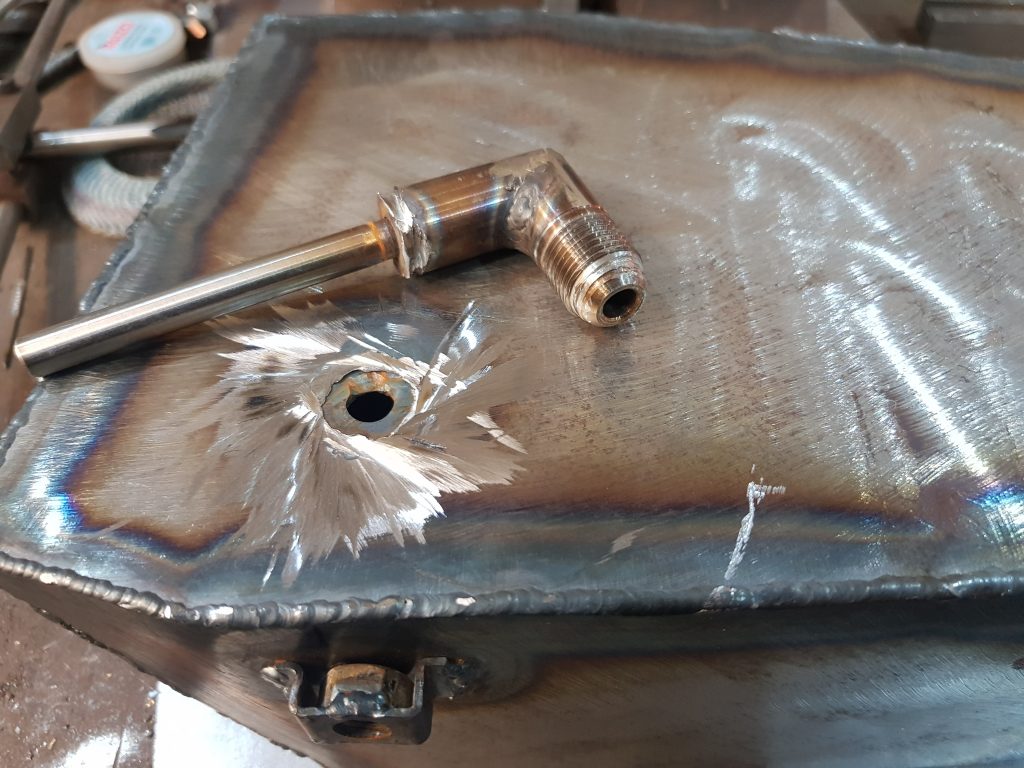
Bit of a mess but fixable, thats the beauty of welding, just keep poking in filler wire to cover up your mess!
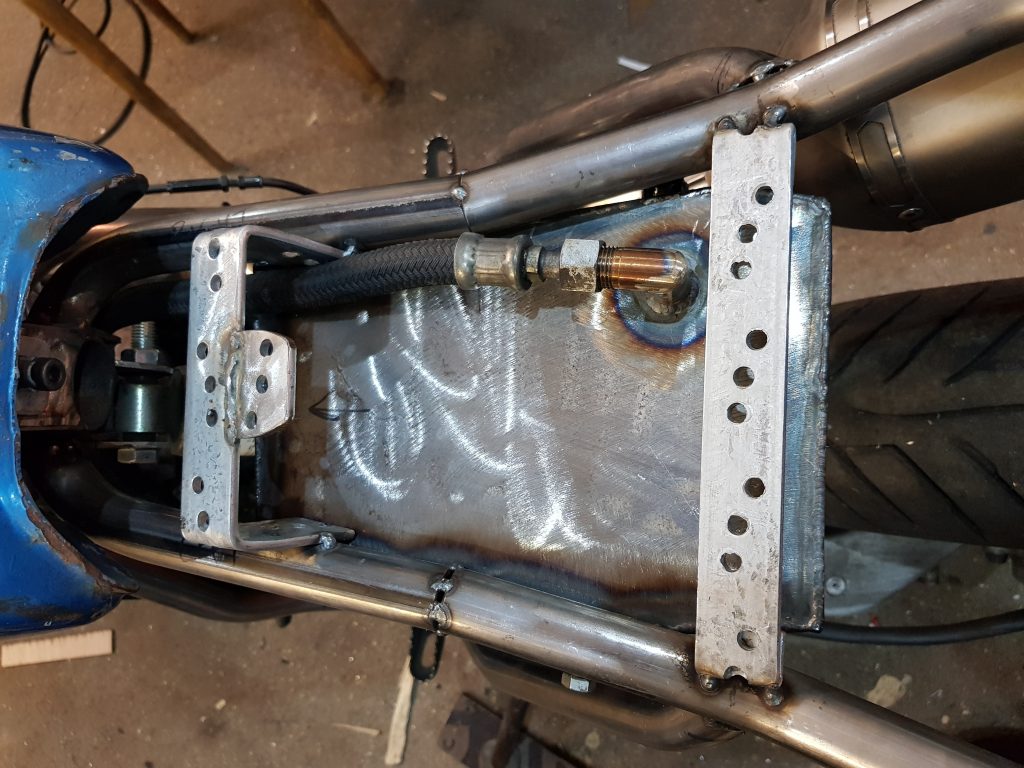
So we have missed the frame this time, much better, now we need a way to fill the tank, had a rummage around and I’ve found an oil bung from a car, looks new!
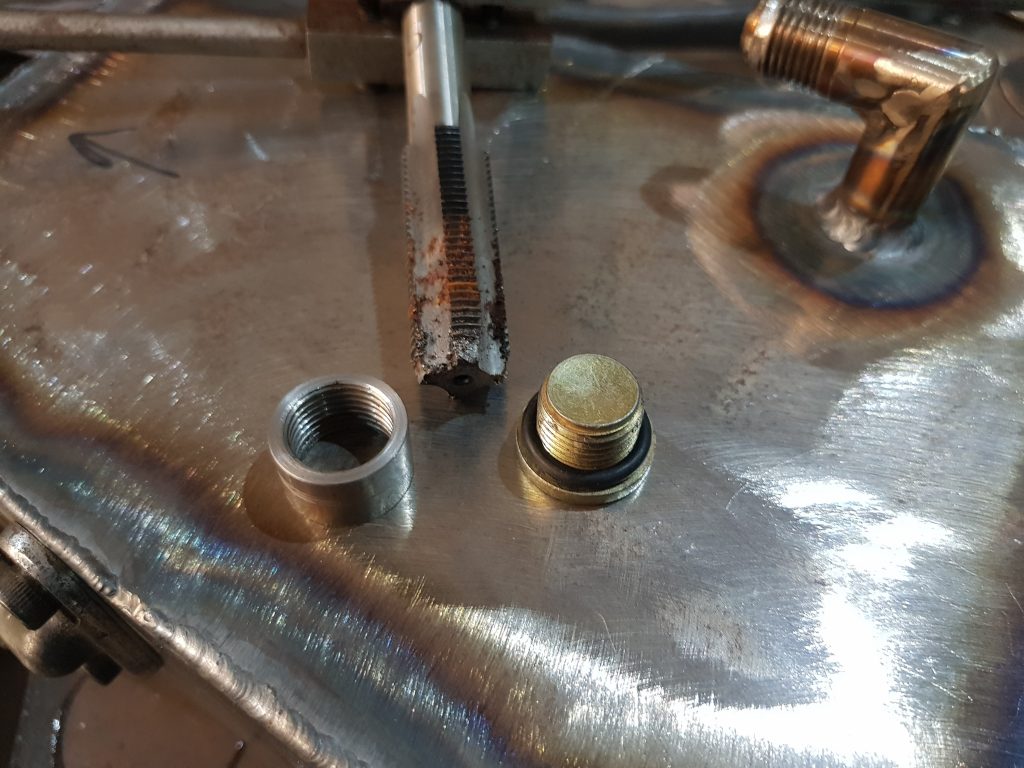
Found a rubber ring that fits and quickly whipped up a threaded jobbie on the lathe, turns out the thread is the same as the elbow so I already had a tap to suit, a little rusty but it worked fine.
I’ll weld it in place tomorrow, need to make some kind of drain plug then I can weld the bottom on the tank. I want to add a magnet to the drain plug as I think it’s a great way to get an early warning if something is letting go internaly.